Welding is a fundamental skill in automotive repair, essential for tasks ranging from bodywork restoration to structural frame repairs. Understanding the various welding techniques and their applications can help ensure high-quality, durable repairs. This blog will delve into the common welding techniques used in automotive repair, including their processes, advantages, and specific applications.
1. MIG Welding (Metal Inert Gas Welding)
Process:
MIG welding, also known as Gas Metal Arc Welding (GMAW), involves feeding a continuous solid wire electrode through a welding gun into the weld pool, joining the base metals together. The process is shielded by an inert gas, typically argon or a mixture of argon and carbon dioxide, to protect the weld from contamination.
Advantages:
- Ease of Use: MIG welding is relatively easy to learn and is often the first welding technique taught to beginners.
- Speed: This method is faster compared to other welding techniques, making it suitable for high-volume production environments.
- Versatility: It can be used on various metals, including steel, aluminum, and stainless steel.
Applications in Automotive Repair:
- Body Panels: MIG welding is commonly used for welding thin sheet metal on car bodies due to its ability to create smooth, clean welds.
- Exhaust Systems: This technique is also effective for repairing or replacing sections of the exhaust system.
2. TIG Welding (Tungsten Inert Gas Welding)
Process:
TIG welding, or Gas Tungsten Arc Welding (GTAW), uses a non-consumable tungsten electrode to produce the weld. The weld area is protected from atmospheric contamination by an inert shielding gas, usually argon. Filler metal, if used, is fed manually into the weld pool.
Advantages:
- Precision: TIG welding offers excellent control and precision, producing high-quality, clean welds.
- Versatility: It can weld a wide range of metals, including aluminum, magnesium, and stainless steel.
- Quality: TIG welds are highly durable and aesthetically pleasing.
Applications in Automotive Repair:
- Frame Repairs: TIG welding is often used for welding structural components due to its strong and precise welds.
- Aluminum Parts: Given its ability to handle aluminum effectively, TIG welding is suitable for repairing aluminum body panels and engine components.
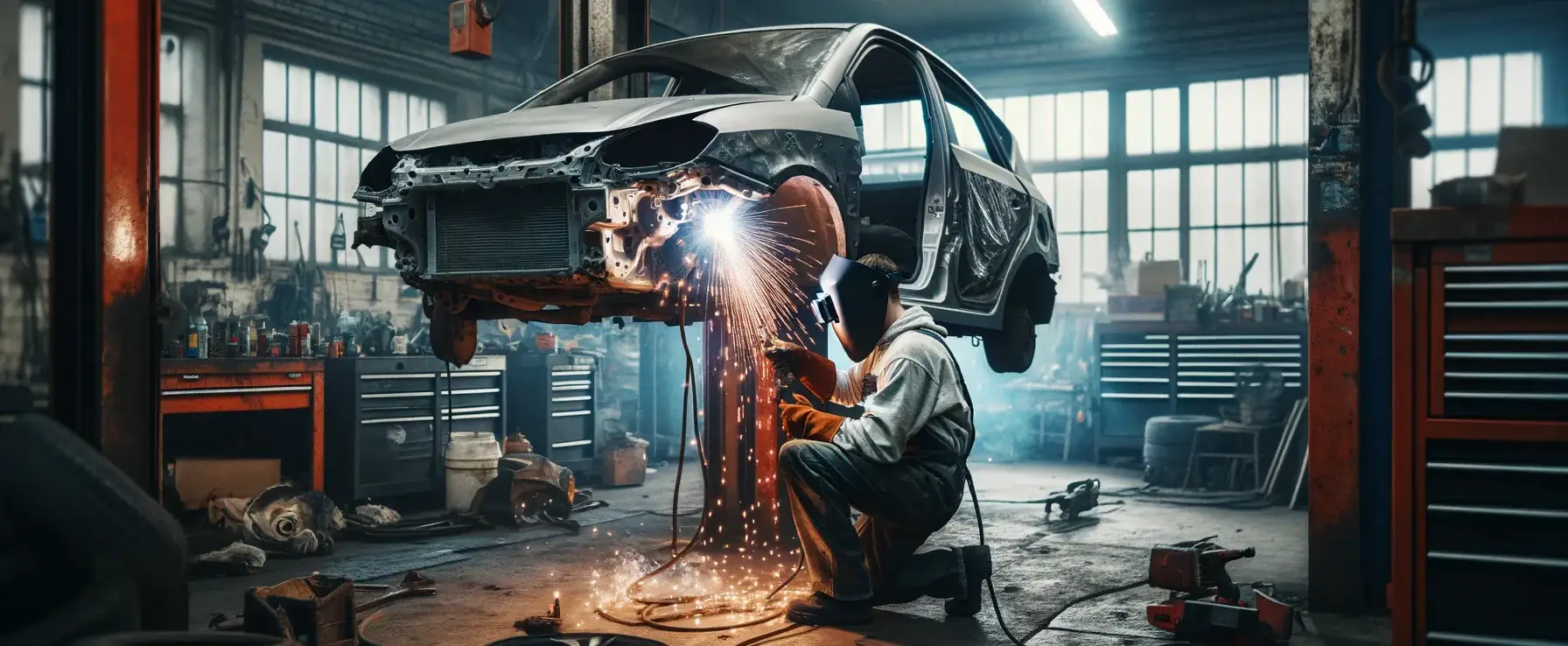
3. Spot Welding
Process:
Spot welding is a type of resistance welding where two metal surfaces are joined by applying pressure and passing an electric current through the metal at the weld spot. This technique is commonly used to join overlapping sheets of metal.
Advantages:
- Speed: Spot welding is a fast process, ideal for production environments.
- Automation: It can be easily automated for consistent and repeatable welds.
- Minimal Distortion: Spot welding causes minimal distortion to the surrounding metal.
Applications in Automotive Repair:
- Body Assembly: Spot welding is extensively used in the automotive industry for assembling car bodies, including joining body panels and structural components.
- Sheet Metal Repairs: It is also suitable for repairing areas where the metal overlaps, such as door skins and trunk panels.
4. Oxy-Acetylene Welding
Process:
Oxy-acetylene welding, or gas welding, uses a flame produced by burning a mixture of oxygen and acetylene gas to melt the base metal and create a weld. Filler metal can be added manually if needed.
Advantages:
- Versatility: This technique can be used for welding, cutting, and brazing various metals.
- Portability: Oxy-acetylene welding equipment is portable, making it suitable for on-site repairs.
- No Electricity Required: It does not require an electrical power source, making it useful in remote locations.
Applications in Automotive Repair:
- Exhaust System Repairs: Oxy-acetylene welding is often used for cutting and welding exhaust pipes.
- Body Repairs: It can be used for welding sheet metal, particularly in older vehicles where traditional techniques were used.
5. Stick Welding (Shielded Metal Arc Welding)
Process:
Stick welding, or Shielded Metal Arc Welding (SMAW), involves using a consumable electrode coated in flux to lay the weld. An electric current is used to create an arc between the electrode and the metal to be welded, which melts the metals and the electrode to form the weld.
Advantages:
- Versatility: Stick welding can be used on a variety of metals and thicknesses.
- Simplicity: The equipment is relatively simple and inexpensive.
- Portability: It is suitable for outdoor and remote welding applications due to its portability and independence from shielding gas.
Applications in Automotive Repair:
- Frame Repairs: Stick welding is suitable for welding thicker sections of the vehicle frame and other heavy-duty components.
- Repairing Rusted Areas: It can be used to weld patches into rusted areas of the vehicle body.
Choosing the Right Welding Technique
The choice of welding technique in automotive repair depends on several factors:
- Material Type: Different welding methods are better suited for specific materials (e.g., aluminum vs. steel).
- Component Thickness: The thickness of the metal affects the choice of welding technique.
- Weld Quality Requirements: Some techniques produce cleaner and more aesthetically pleasing welds.
- Accessibility: Certain areas of the vehicle may be easier to weld using specific techniques.
Conclusion
Welding is an indispensable part of automotive repair, offering solutions for various repair and restoration tasks. Understanding the common welding techniques—MIG welding, TIG welding, spot welding, oxy-acetylene welding, and stick welding—enables automotive professionals to choose the appropriate method for each job. By selecting the right welding technique, mechanics can ensure strong, durable, and high-quality repairs that extend the life and enhance the performance of the vehicle.
FAQs
Which welding technique is best for automotive bodywork?
MIG welding is often preferred for automotive bodywork due to its ease of use, speed, and ability to produce clean welds on thin sheet metal.
Can I use TIG welding for repairing aluminum parts in my car?
Yes, TIG welding is ideal for aluminum repairs due to its precision and ability to produce high-quality welds on aluminum and other non-ferrous metals.
What are the signs that my car's suspension needs repair?
Common signs include a rough ride, drifting or pulling to one side, uneven tire wear, excessive bouncing, and leaking fluid from shock absorbers or struts.
Master Automotive Welding with Professional Training
Enhance your automotive repair skills by mastering various welding techniques. Contact us today for professional training and certification programs tailored to your needs.